Of all the various factors that can affect the performance and life expectancy of a mechanical seal (and there are many), the operating temperature is one of the most critical, and is a vital factor to consider. This is true for more than simply the selection of seal type and materials however; it is also a factor that should be considered by those operating the equipment or examining a leaking seal.
The reason for this is simple: Temperature can have a wide variety of effects on a mechanical seal. However, exactly which effects will manifest in a given scenario depends on other factors, such as the nature of the product, environmental temperature, pump curve, etc. This can be helpful when performing a failure analysis, as the precise effects that occur can be used to narrow down the nature of the problem.
Direct Effects Of Temperature
The simplest type of effect that temperature can have on a seal is thermal expansion/contraction. Higher temperatures cause materials to expand, while lower cause shrinkage; both of which can affect critical components in unfortunate ways if they exceed the range the seal is designed to tolerate.
Some common examples of this are:
- Thermal Shock – Seal faces can fracture from sudden and rapid cooling of a heated component.
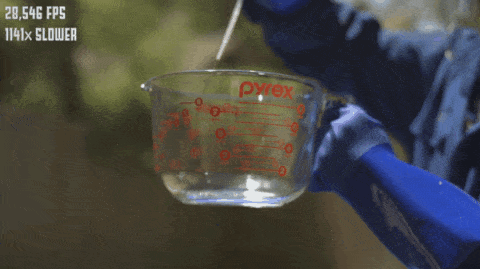
- Heat Checking – cracking due to differential between thermal expansion coefficients in alloys and other composite materials, such as tungsten carbide. Most commonly occurs on seal faces.
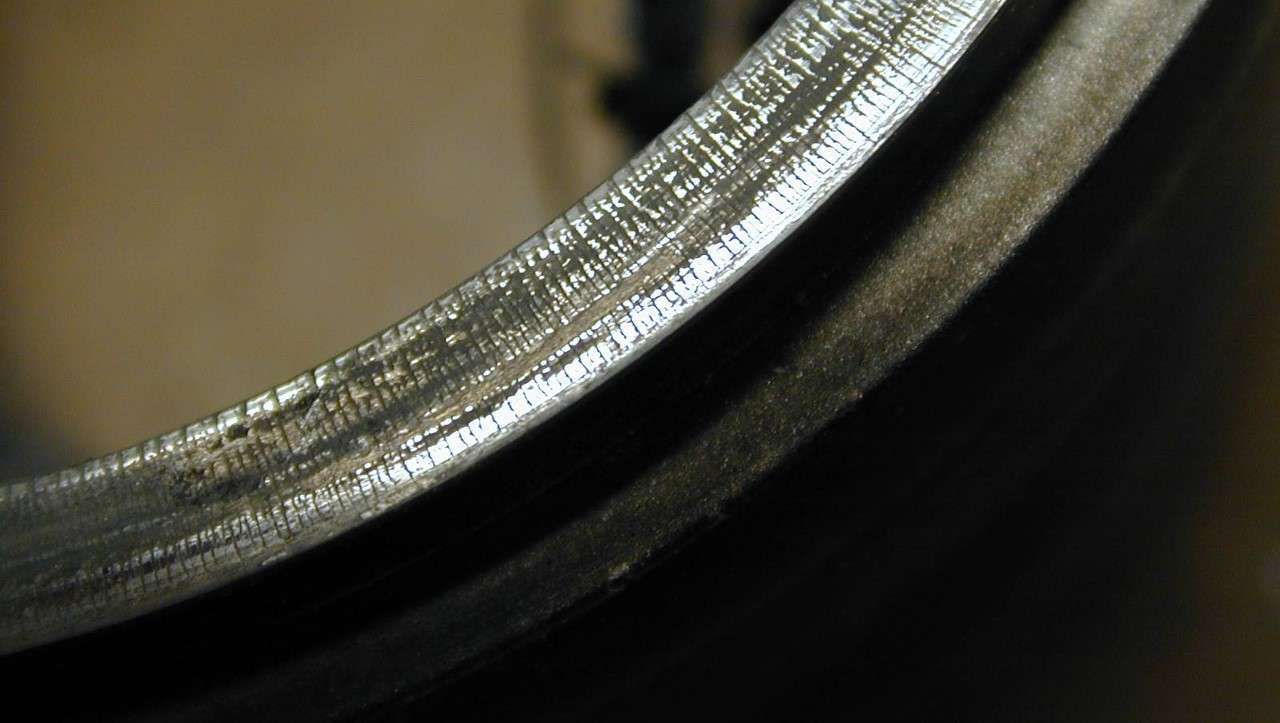
- O-ring thermal damage due to elevated temperatures.
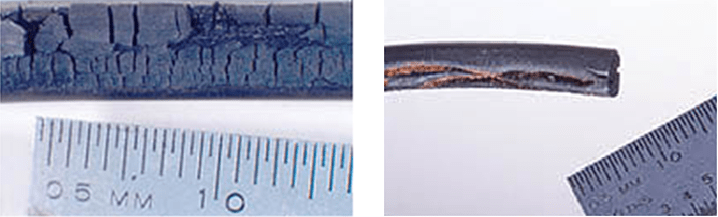
Other common issues include:
- Loosening or loss of press fit on seal faces and other components.
- Expansion of O-rings can cause seal faces to crack due to imparted stresses.
- Seal face hang-up due to excessive drag from an enlarged dynamic O-ring no longer being allowed to move.
- O-ring brittleness due to very low temperatures.
- Face warping due to very low or high temperatures.
Indirect Effects of Temperature
Besides the direct negative effects, excessively low or high temperature can also cause problems with a mechanical seal indirectly. For example, high temperatures can dramatically increase chemical aggression versus metal parts, elastomers, and even seal faces. A common rule of thumb is that reactivity doubles every 18 degrees Fahrenheit (10 degrees Celsius).
Depending on the service, temperature can also cause changes to the physical properties of the product being pumped, or even the barrier fluid. For example, products or barrier fluids with a high viscosity at ambient temperature can cause some face materials to blister due to fluid shear forces at the seal faces. This is common in services with high operating temperatures, and often necessitates pre-heating or heat tracing the pump and/or seal pot.
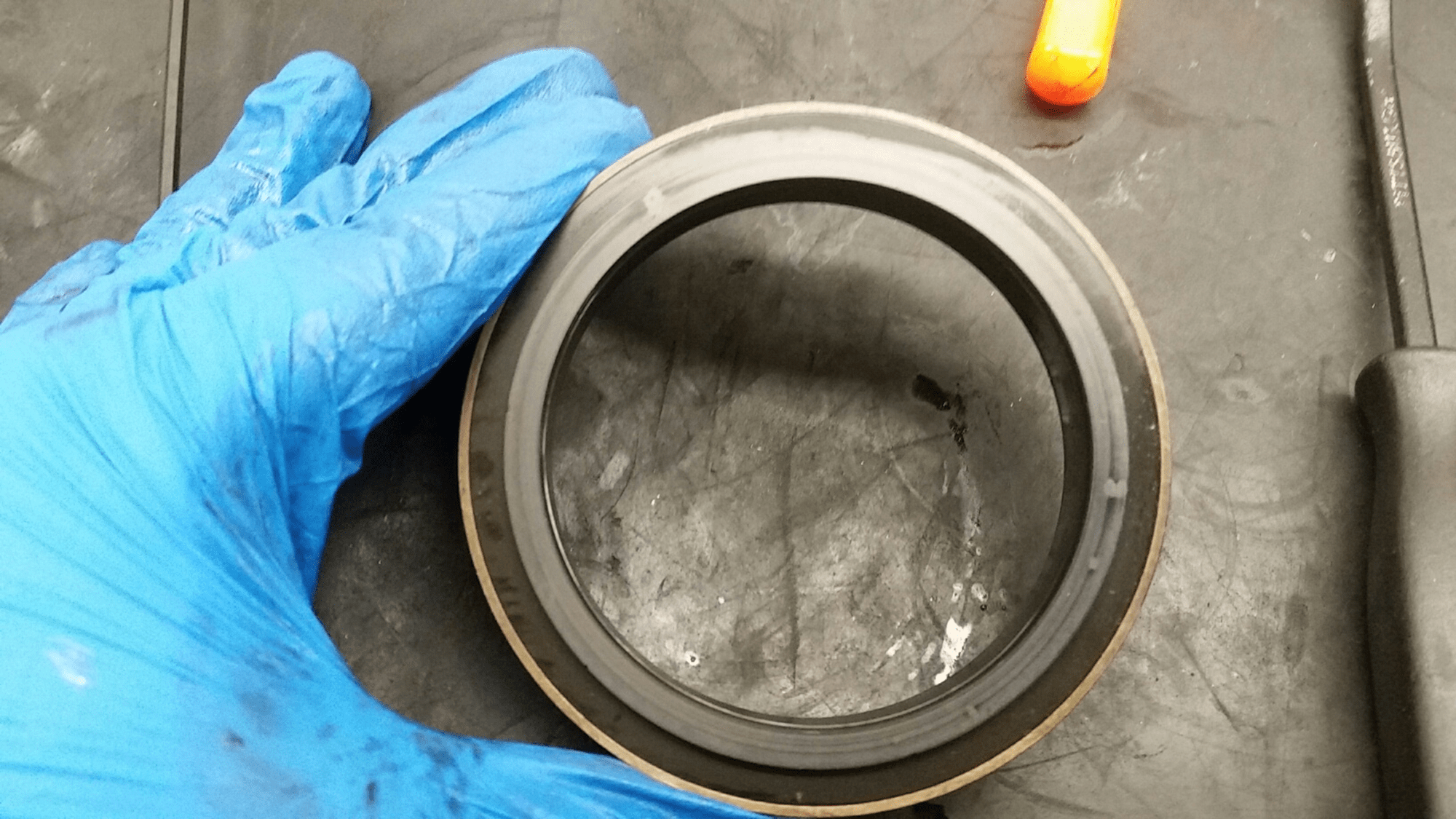
Temperature can also affect the state of the product, which can have a negative impact on both pumps and seals. For example, if a hydrocarbon service such as liquefied natural gas or similar is not kept sufficiently cool for a given pressure, it will vaporize. These services are oftentimes high pressure, and it is common to use a dual, unpressurized (tandem) seal arrangement (e.g. API Plan 52). Since the process side pressure is higher, the inboard/inner faces are lubricated by the minimal leakage across the sealing gap. However, as the product vaporizes, the inboard faces receive less lubrication and experience dry running, which results in rapid face wear.
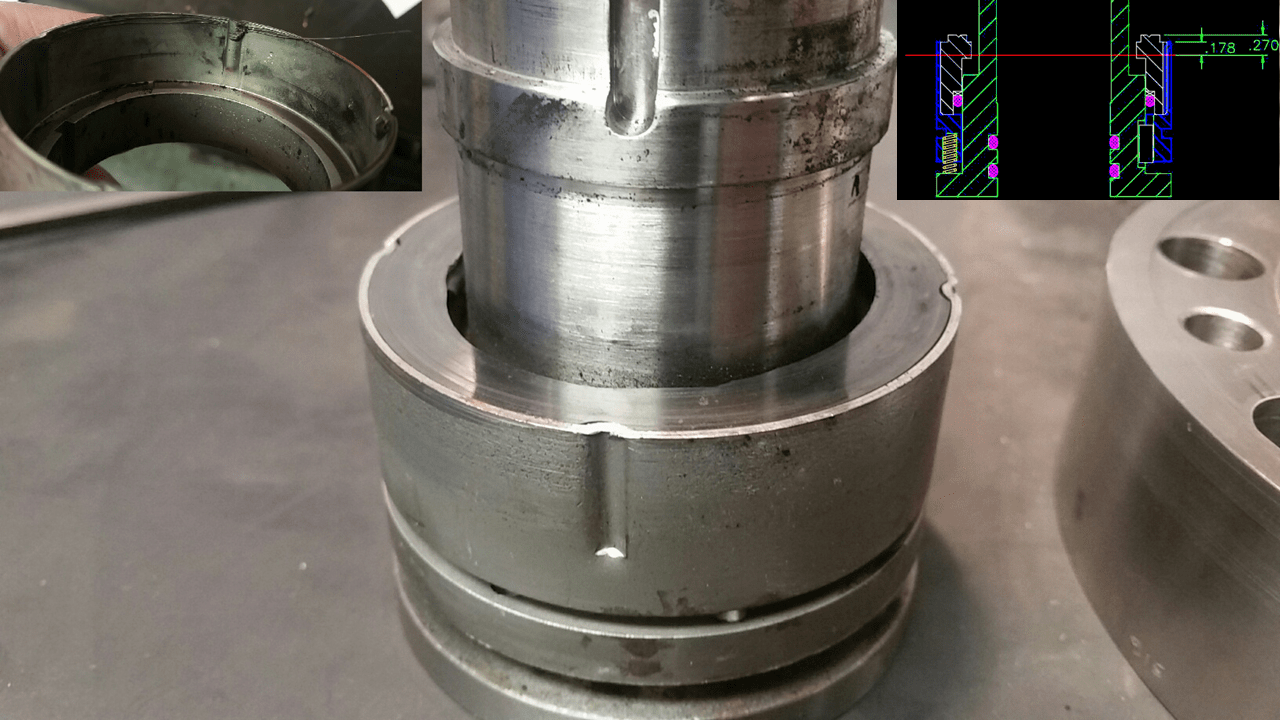
Common Causes & Solutions
Temperature related issues can have a variety of root causes. As a result, there are also a wide variety of methods which have been developed to deal with them. The solution in a given scenario can sometimes be as simple as changing a startup procedure, but in some cases may necessitate changes to the seal design, or the addition of external cooling or heating.
A common example of this is running a pump dead headed (discharge closed or insufficient outflow), or off the curve (cavitation, low NPSH, etc.) The solution may be to change how the equipment is operated, but depending on the situation, may require changes to the system itself, such as moving the pump to a lower area or changing to a larger/smaller pump.
Some other common problems include:
- Pump running dry: Often an operational issue, can be mitigated with electric load monitoring on the motor.
- Heat Exchanger Problems: It is important that a heat exchanger is properly sized for the application, as well as receiving sufficient flow. As such, it is important to regularly check for clogs and clean/replace the heat exchanger when necessary.
- Loss of API Plan 32 (injection of clean cool fluid from an external source to the seal chamber): Plan 32 is often used to isolate seals from products that are hot, abrasive, or have poor lubricity. The loss of it will cause the seal to experience these conditions, which may damage the seal or cause thermal shock when the Plan 32 supply is restored.
- Incorrect tubing configuration for Seal Pot (API Plans 52, 53A): This can prevent proper circulation of fluid, reducing seal heat dissipation. Ensure tubing connections are as short as possible, and follow guidelines for a gentle slope with no dips.
- Excessive Axial Loading: Increases frictional heat generation at the seal faces, and may indicate a bearing problem or other similar mechanical issue.
- Exterior Environmental Temperature: Intense heat and cold due to seasonal changes can often cause a variety of problems if they are not accounted for. This type of issue is something that must be addressed by preparation prior to the event, or accounted for when the system and seal are engineered.
AFTERWORD
Temperature is a vital factor to consider during not only the design of a mechanical seal, but also during operation and failure analysis. It can have a variety of effects on mechanical seals depending on the scenario, and as such can be useful for pinpointing the precise cause of failure. However, it is also up to equipment operators to consider potential situations that may result in failures and take measures to prevent or mitigate them. With proper care and consideration of the various factors that affect performance, seal life can be significantly extended.