Mechanical seals consist of multiple components critical to successfully preventing leakage of the pumped process fluid. Material selection of seal faces, secondary sealing members, and metal components all factor in to how long a mechanical seal will properly operate.
The components making up the mechanical seal differ based on the seal type. Process fluid chemical properties determine seal selection as well as temperature, pressure, and API requirements.
Single, pusher mechanical seals like the 1500E are the most common seal type. A pusher seal is any seal that uses springs with a dynamic O-ring. Single seals provide one set of seal faces between the process fluid and atmosphere, so all materials are considered in contact with the process fluid. Many single seals include a non-sparking throttle bushing in the seal gland to help minimize leakage in the event of a seal failure. The 1500 in Figure 1 is an example of a single, pusher seal with a throttle bushing.
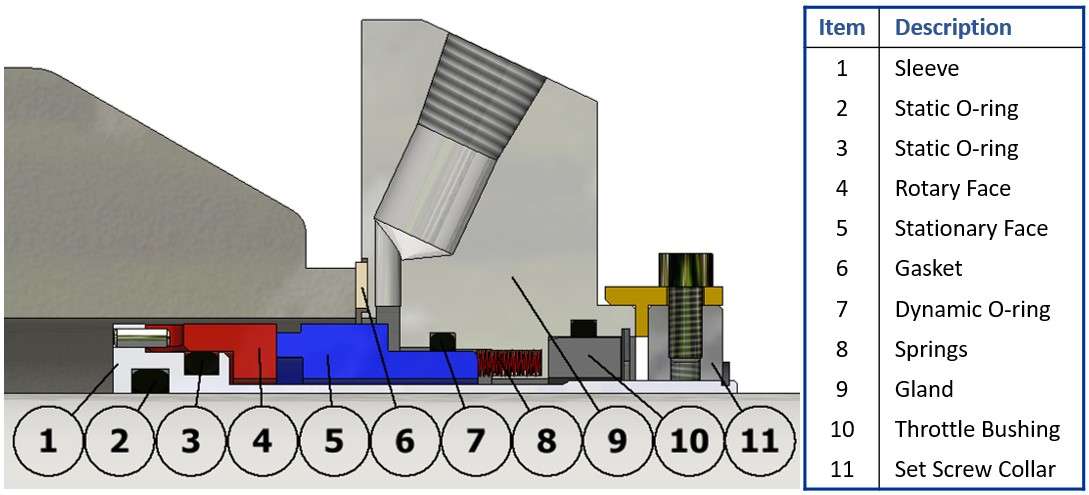
Figure 1: Parts Identification of a 1500 Single Pusher Seal
When a throttle bushing is not considered sufficient to prevent leakage to atmosphere, a dual mechanical seal may be considered. Dual mechanical seals offer two sets of seal faces between the process fluid and atmosphere, like the P-3F shown in Figure 2. Buffer or barrier fluid fills the cavity between the two sets of seal faces. The P-3F is also an example of a pusher seal with springs and dynamic O-rings.
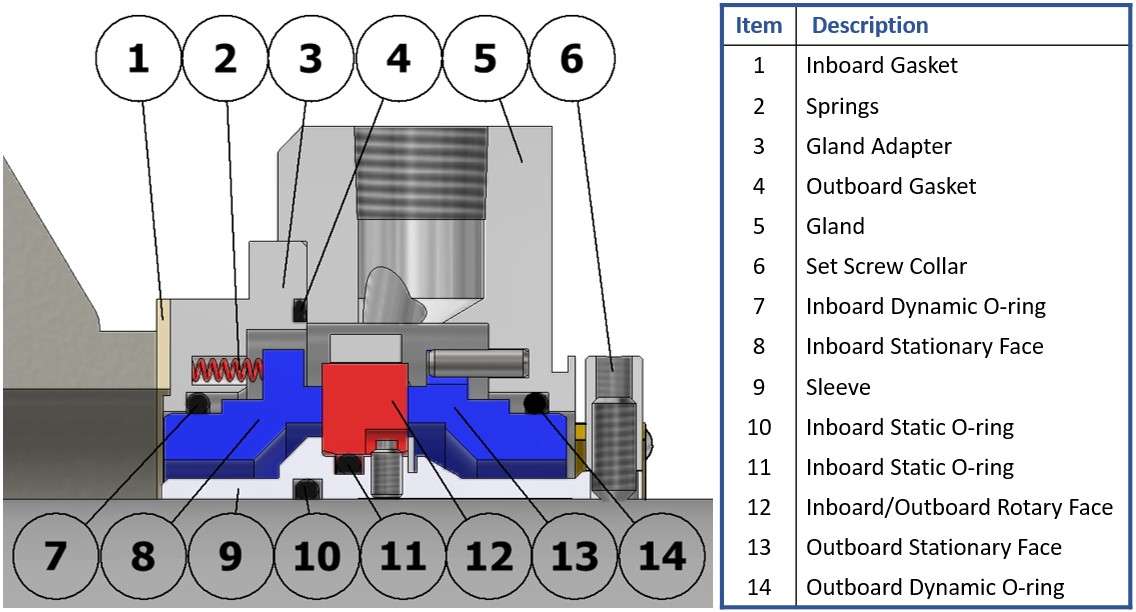
Figure 2: Parts Identification of a P-3F Dual Pusher Seal
Non-pusher style seals have no dynamic O-rings like the seal shown in Figure 3, which uses welded metal bellows in lieu of springs. The Ultraseal 789 is also an example of a high-temperature metal bellows seal, which uses flexible graphite packing as secondary sealing members in lieu of O-rings or PTFE-based gaskets.
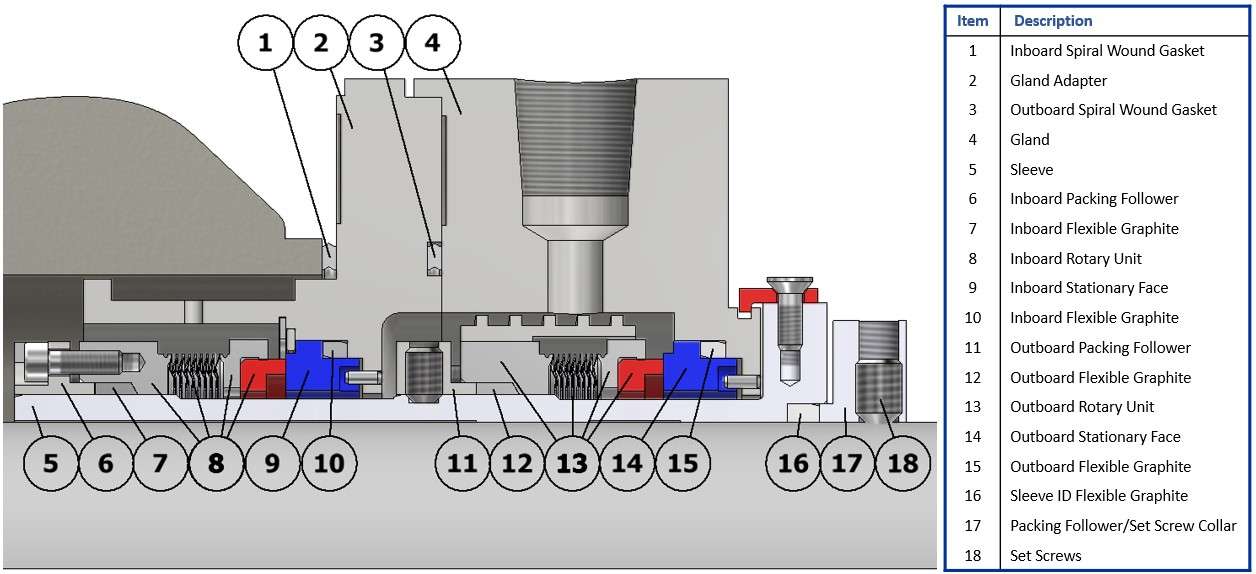
Figure 3: Parts Identification of an Ultraseal 789 High-Temperature Metal Bellows Dual Seal
Dual seals like the P-3F in Figure 2 and the Ultraseal 789 in Figure 3 have wetted and non-wetted components. Wetted components contact the process fluid and include the gland adapter, sleeve, inboard seal faces, and inboard secondary sealing members.
In certain dual seal applications, the non-wetted seal components will never contact the process fluid during normal seal operation. Non-wetted materials in these applications often do not need to meet the same requirements for heat and corrosion resistance. As a result, more cost-effective materials with greater availabilities may be used. However, seal designers must still consider the barrier/buffer fluid properties.
Seal designers must select materials sufficient for the process fluid and barrier/buffer fluid chemical properties, pressure, temperature, and viscosity while maintaining the affordability and availability of the mechanical seal.
Seal Faces
The most critical sealing components of mechanical seals are the seal faces themselves. Each set of mechanical seal faces consists of one rotating face and one stationary face. The faces can be referred to many ways (rotary face vs stationary face, rotor vs stator, washer vs seat, mating ring vs primary ring), but the function is the same. One seal face will mount to and rotate with the pump shaft. The other seal face remains stationary and independent of shaft rotation by mounting to the seal gland.
Seal faces are manufactured with a controlled, flat surface where the two seal faces contact during pump operation. The flat surfaces allow a fluid film to form between the two seal faces for lubrication. Even with the fluid film lubrication, the faces will still contact each other causing wear and heat generation.
Most mechanical seals will consist of one softer wearing face and one hard counter face. Depending on the mechanical seal type, the wearing face can be either rotating or stationary. For the 1500 in Figure 1 and P-3F in Figure 2, the wearing face is the stationary face. However, the Ultraseal 789 shown in Figure 3 uses a rotary face as the wearing face.
When selecting seal face materials, the faces’ mechanical, thermal, and wear properties, along with chemical resistance, must all be considered.
Seal Face Materials
Carbon Graphite
Most mechanical seals use carbon graphite blends for the wearing face material, which are desirable for their general chemical inertness and self-lubricating properties. Carbon graphite materials are manufactured through blending various amorphous carbon and graphite sources, which results in a soft and porous structure. Due to these inherent traits, the carbon graphite structure must then be impregnated with a filler, typically a resin or a metal, to improve the impermeability and mechanical properties of the face. The composition of the original carbon graphite mixture and the impregnant determine the material properties of the seal faces. See Table 1 for some of the different carbon seal face grades PPC offers.
Table 1: PPC Carbon Grades
Carbon Grade | Description | Max Temperature |
---|---|---|
#9 | Standard Grade Resin filled FDA grade | 500°F (260°C) |
#10 | Standard API Grade Antimony filled Blister resistant | 700°F (370°C) |
#12 | Antimony filled Used for lift-off gas seal applications | 700°F (370°C) |
#14 | Premium resin filled High service duty FDA grade | 500°F (260°C) |
#15 | Resin filled Excels in dry-running mixer seals FDA grade | 500°F (260°C) |
PPC uses a resin filled carbon graphite (#9 Carbon) for our standard grade of carbon seal faces. Resin carbons have a broad range of chemical compatibility and provide an excellent balance of material benefits and cost. Our #9 Carbon is also FDA grade and is thus suitable for industries requiring this approval.
API 682 states that any carbon graphite faces used shall be premium grade and blister-resistant. PPC’s standard API 682 carbon graphite grade is #10 Carbon, which has an antimony metal filler. In addition to the blister resistance, antimony impregnated carbon graphite fares better in higher temperature and pressure applications. Antimony impregnated carbon graphite faces are also preferred in low specific gravity and partial dry running applications due to better self-lubricating properties.
Some applications, such as gas seals, require a carbon graphite face to run in contact without liquid lubrication. PPC offers special dry-running grades of carbon for these designs. Dry-running carbon graphite grades are manufactured with unique compositions and film-forming additives to improve performance. As a result, the carbon graphite face offers better self-lubricating properties but may come at a premium price point, and other mechanical properties of the material may be more limited.
Resin and metal impregnants are prone to corrosion in some aggressive acid applications. Acid grade carbon graphite faces are available that have no resin filler. As a result, acid grade carbon graphite faces can be used in highly corrosive applications though they lack the strength of other carbon graphite grades. However, with the development of direct sintered silicon carbide, acid grade carbon graphite has seen a large decline in use.
Silicon Carbide
Silicon carbide is the most common material selected for hard faces. The benefits of silicon carbide as a face material include high thermal conductivity, abrasion resistance, and chemical resistance. PPC offers several grades of silicon carbide including reaction bonded, direct sintered, and graphite loaded variants.
Reaction bonded silicon carbide is manufactured through a reaction of silicon metal with carbon graphite particles. The manufacturing process results in the presence of 8-12% free silicon metal in the final product. Although reaction bonded silicon carbide has excellent wear and lubrication properties, the presence of free silicon limits chemical resistance. Reaction bonded silicon carbide should be avoided in applications with the presence of strong acids and strong bases. As a rule of thumb, reaction bonded silicon carbides should not be used in applications with a pH less than 4 or greater than 11.
Direct sintered silicon carbide (also called self-sintered silicon carbide) offers greater chemical resistance. Pure silicon carbide powder is sintered using nonoxide aids and results in an almost entirely silicon carbide material. Without the presence of free silicon metal, the direct sintered silicon carbide faces are resistant to most chemicals and can be used in almost any mechanical seal application.
Graphite loaded silicon carbide can be made with either reaction bonded or direct sintered silicon carbide. The primary purpose of graphite loaded silicon carbide is to increase the lubrication properties of silicon carbide seal faces using free graphite inclusions dispersed in the silicon carbide structure. Graphite loaded silicon carbide may provide increased performance in applications where hard faces must be used and lubrication is limited.
Diamond coating
One of the newest innovations in mechanical seal face materials, diamond coated silicon carbide offers a harder seal face with high thermal conductivity and low friction. Diamond coated silicon carbide’s increased hardness allows for use in abrasive services, and the combination of high thermal conductivity and low friction greatly reduces seal generated heat, which is ideal for low lubrication or dry-running applications.
In addition to the more traditional Chemical Vapor Deposition (CVD) diamond coating, which adds a layer of diamond film, PPC offers a proprietary surface conversion reaction where a portion of the silicon carbide face is converted to diamond. Although diamond coating has a high upfront cost, the increased seal performance may save money over the long run.
Tungsten Carbide
Tungsten carbide is another common hard face material. These faces are manufactured by pressing a tungsten carbide powder into a shape and binding the carbide particles using a secondary metal. Historically, tungsten carbide was bound using cobalt, but nickel bound tungsten carbide is more common now due to broader chemical resistance.
Although tungsten carbide does not offer the same abrasion or chemical resistance as silicon carbide, tungsten carbide is advantageous in applications where increased strength is preferred. Tungsten carbide is not as fragile as silicon carbide and fares better in pumps with more vibrations.
Most seals PPC offers use monolithic face designs, meaning that the face material is made entirely of one material without any shrink fit bodies or coated overlays. However, some seals such as the Ultraseal 789 in Figure 3 require the face material to be pressed into a metal holder. Due to silicon carbide’s lower strength, the compressive force of the metal holder must be reduced and faces limitations in some higher temperature applications.
Table 2: Temperature Limitations of Common Hard Face Materials
Construction | Max Temperature |
---|---|
Solid Tungsten Carbide Ring | 750 (400°C) |
Tungsten Carbide Ring Pressed into 316SS Body | 500°F (260°C) |
Tungsten Carbide Ring Pressed into Alloy C-276 Body | 500°F (260°C) |
Tungsten Carbide Ring Pressed into 17-4PH SS Body | 700°F (370°C) |
Tungsten Carbide Ring Pressed into Alloy 42 Body | 750°F (400°C) |
Solid Silicon Carbide Ring | 800°F (427°C) |
Silicon Carbide Ring Pressed into 316SS Body | 200°F (93°C) |
Silicon Carbide Ring Pressed into Alloy C-276 or 17-4PH SS Body | 250°F (120°C) |
Silicon Carbide Ring Pressed into Alloy 42 Body | 750°F (400°C) |
Other seal Face materials
Although the majority of PPC’s seals today use some sort of combination of carbon graphite with silicon carbide or tungsten carbide, PPC offers other seal face materials. Historically, mechanical seals have used ceramic or metal faces, and many modern mechanical seals still use these faces.
Before discovering the benefits of silicon and tungsten carbides as seal faces, many mechanical seals used ceramic seal faces. Ceramic faces, such as aluminum oxide, are still common in some lower-duty applications where low cost is paramount. However, ceramic faces have poor thermal conductivity compared to carbides and may cause an increase in seal generated heat. Ceramic faces should only be considered in applications with low pressure, temperature (less than 350°F), and speed.
When it comes to metallic face materials, bronze is softer and more compliant, and leaded versions provide some limited lubricating properties. However, bronze faces do not offer great thermal conductivity, and the face will often distort during service, providing potential leak paths across the seal face. Some applications still use bronze seal faces, but bronze mostly fell out of favor when the benefits of carbon graphite and carbide faces were discovered.
Ni-Resist is an austenitic cast iron with nickel and offers limited corrosion resistance. Generally, Ni-Resist may be used in water services but should not be used in any aggressive applications or temperatures greater than 350°F.
Stellite® is a cobalt-chromium alloy metal with good wear capabilities. When used as a seal face material, Stellite® is commonly welded to a 316SS base. Stellite® does not offer the temperature capabilities of other seal face materials (max temperature: 350°F) and is more prone to thermal distortions and heat checking. However, Stellite® faces are still common in large mixer seals with low RPM where size makes carbide faces cost prohibitive.
Metallurgy
Mechanical seals use metals extensively from springs to the seal gland. The major metal components include the seal gland/gland adapter, sleeve, and seal face retainers. For these metal parts, the main factors for metal selection are corrosion resistance and cost.
PPC uses 316SS for most metal components. 316SS offers excellent corrosion resistance, machinability, strength, and availability while staying cost effective.
Duplex stainless steels are used in sour services and applications with high chloride content. Duplex grades are more resistant to stress corrosion cracking and chloride pitting than 316SS while still offering high strength and machinability. Duplex stainless steels cost more than 316SS but are generally more cost effective than nickel alloys.
Nickel alloys such as Hastelloy®, Alloy-20, Monel®, and Inconel® are used in more aggressive applications. The nickel alloys exhibit better corrosion resistance than stainless steels, especially in high-temperature applications.
Premium metals, such as Titanium and Zirconium, are available in the most aggressive and hottest applications where nickel alloys are prone to corrosion. Titanium and Zirconium are limited to uses where no other metal is acceptable due to their high cost.
Although most mechanical seals use wetted metal components, PPC also offers seal designs with no wetted metal components. These seal designs are used in highly corrosive services where no metal offers sufficient chemical compatibility or to avoid the high cost of premium metal grades.
Springs
Mechanical seals use springs to press the seal faces together during the absence of hydraulic pressure while also adjusting for wear and misalignment. Most modern seals use multi-spring seal designs, but single spring designs still exist. Material selection must also consider spring location. The 1500 (Figure 1) and the P-3F (Figure 2) use non-wetted springs, but wetted springs are common on API 682 style seals. Wetted springs need to factor in chemical compatibility with the process fluid. Most multi-spring seal designs use Hastelloy-C® springs, but 316SS springs may also be used for suitable applications. Single spring designs typically use 316SS, as the larger wire diameter mitigates corrosion concerns.
Metal Bellows
Many mechanical seals use welded metal bellows seals rather than coil spring designs. Metal bellows seals are used in applications where either seal O-ring hang-up is a concern or applications where high temperatures prevent the use of elastomers. See the Ultraseal 789 in Figure 3 for an example of a high temperature cartridge metal bellows and Figure 4 for an example of a typical metal bellows rotary unit.
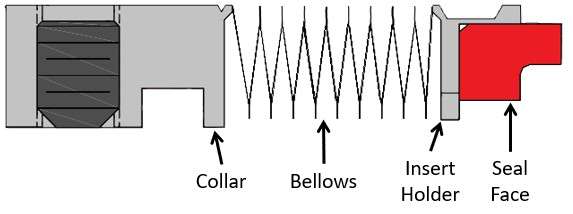
Figure 4: Typical Bellows Rotary Unit
Welded metal bellows material selection depends on the process fluid’s chemical properties and heat. Hastelloy-C® is the most common bellows material due to excellent corrosion resistance and ease of manufacturing. API 682 requirements must also be taken into consideration, which specify different metal bellows materials depending on the seal type. Table 3 lists PPC’s most common metal bellows materials.
Table 3: PPC’s Most Common Metal Bellows Materials
Material | Comments |
---|---|
AM-350® SS | Good chemical resistance Good for high temperature applications |
Hastelloy-C® | Standard for 1500ERB, Ultraseal 2000, and API 682B Seals Excellent corrosion resistance Good for high temperature applications |
Inconel 718® | Standard for API 682C Seals Excellent corrosion resistance Best for high temperature applications |
Alloy 20 | Less common bellows material Excellent corrosion resistance Good for high temperature applications |
Insert Holders
Some seal designs, including metal bellows mechanical seals, require the seal face to be pressed into a metal insert holder with an interference fit to prevent a leak path. Seal designers must consider the coefficient of thermal expansion when choosing insert holder material as well as corrosion resistance for the application. Common insert holder materials are:
- 316SS
- Hastelloy-C®
- Invar®
- Alloy-42
Invar® or Alloy-42 are preferred in high temperature seal applications due to a low coefficient of thermal expansion. The selection of Invar® versus Alloy-42 mainly depends on the process temperature based on differing coefficients of thermal expansion.
Reference Table 2 for temperature limits for designs with tungsten carbide and silicon carbide inserts.
Set Screws
Set screw material selection depends on location and function within the seal. Many cartridge mechanical seals will include set screws on the rotary units that are set on the mechanical seal sleeve. These set screws are considered a wetted metal and will need to match the material of other wetted metal components.
Most cartridge mechanical seals drive seal rotation by using a set screw collar to affix the seal to the pump shaft. Drive collar set screw material will consider the pump shaft/sleeve material in addition to corrosion resistance. The set screws should be of greater hardness than the pump shaft/sleeve to ensure the drive collar has enough bite to drive the mechanical seal cartridge. Corrosion is less of a concern in these non-wetted locations but should be closely evaluated in coastal or marine environments.
Common set screw materials include:
- 316SS
- Heat treated alloy steel (often Zinc plated)
- Heat treated 416SS
- Hastelloy-C®
- Alloy-20
Secondary Seals
Secondary seals prevent leakage between components of mechanical seals. These can include O-rings, gaskets, and flexible graphite packing in some mechanical seals. Seal designers need to consider stuffing box pressure, chemical resistance, and temperature for secondary seals. Table 4 lists several common secondary seal materials and their temperature limitations.
Table 4: Temperature Limitation of Common Secondary Seals
Material Compound | Min. Temp. Limit | Max. Temp. Limit |
---|---|---|
FKM (Fluoroelastomer) | 0°F (-18°C) | 400°F (204°C) |
EPDM | -40°F (-40°C) | 250°F (121°C) |
BUNA N(Nitrile) | -40°F (-40°C) | 225°F (107°C) |
AFLAS® | 32°F (0°C) | 450°F (232°C) |
CHEMRAZ(505)® | -22°F (-30°C) | 446°F (230°C) |
CHEMRAZ(615)® | 0°F (-18°C) | 615°F (324°C) |
KALREZ(6375)® | -4°F (-20°C) | 527°F (275°C) |
KALREZ(7075)® | -4°F (-20°C) | 620°F (327°C) |
PTFE ENCAPSULATED FLUOROELASTOMER | -40°F (-40°C) | 350°F (177°C) |
TEFLON® | -350°F (-210°C) | 500°F (260°C) |
GYLON® | -350°F (-210°C) | 500°F (260°C) |
GRAFOIL® | -400°F (-240°C) | 850°F (454°C) |
NASB | -40°F (-40°C) | 700°F (371°C) |
Elastomers
O-rings are the most common type of secondary seals. Most mechanical seals will have static and dynamic O-rings. Dynamic O-rings move relative to the surface they seal against and are commonly used on the spring-loaded mechanical seal face. Static O-rings are all other O-rings that do not move relative to the sealing surface. See Figure 1 and Figure 2 for examples of static and dynamic O-rings. PPC’s most common O-ring materials are:
- Aflas®
- Buna N (Nitrile)
- EPDM
- FKM (Fluoroelastomer)
- FFKM (Perfluoroelastomer)
Each O-ring listed has unique chemical resistances and temperature limitations. For example, FKM has a wide range of chemical compatibility, but does not fare as well in hot water applications compared to EPDM and Aflas®. Knowing the process fluid and temperature are critical for O-ring selection.
FFKM is considered a premium grade elastomer offering greater chemical resistance and wider temperature ranges than other elastomer materials. Chemraz® and Kalrez® are the most common FFKM elastomers used, and both offer several grades with varying chemical resistances for different applications. However, the benefits of FFKM elastomers come with the drawbacks of higher prices and longer lead times.
Non-elastomers
Flexible Graphite
Elastomeric O-rings are not always suitable for high temperature applications. API 682 recommends using flexible graphite (Grafoil®) in seals with applications over 350°F. Grafoil® is a pure graphite that is chemically inert and offers excellent thermal conductivity.
In high temperature seals where Grafoil® is used, the Grafoil® must be compressed using a packing follower on each rotary unit and at the set screw collar. See the Ultraseal 789 in Figure 3 for an example of flexible graphite with packing followers.
Flat Gaskets
Non-API style seals such as the 1500 in Figure 1 and the P-3F in Figure 2 use flat gaskets in most cases. PPC’s standard flat gasket offering is Gylon®, which is a filled PTFE material. Gylon® is a preferred gasket material due to its chemical compatibility and resistance to cold flow and creep. PPC offers Teflon® and asbestos substitute (non-asbestos/NASB) gaskets as well. Each gasket material is inert to the process fluid in most applications.
Spiral wound gaskets of 304SS and Grafoil® are used in applications where high temperatures make other gasket materials unsuitable. See the Ultraseal 789 in Figure 3 for an example of a high temperature seal with spiral wound gaskets.
Conclusion
Each mechanical seal component offers unique challenges when selecting materials. All materials have different advantages for each application, so knowing the process fluid chemical properties and application conditions are critical for selecting the right materials. Using our experience with material combinations and knowledge of the process conditions, PPC aims to select the best materials to balance seal performance and affordability.
Footnotes
- Aflas is a registered trademark of AGC Inc.
- AM 350 is a registered trademark of ATI Properties LLC
- Chemraz is a registered trademark of Greene, Tweed Technologies, Inc.
- Grafoil is a registered trademark of Neograf Solutions, LLC
- Gylon is a registered trademark of Garlock Sealing Technologies LLC.
- Hastelloy is a registered trademark of Haynes International, Inc.
- Invar is a registered trademark of Aperam Alloys Imphy
- Kalrez is a registered trademark of DuPont Polymers, Inc.
- Monel and Inconel are registered trademarks of Huntington Alloys Corporation
- Stellite is a registered trademark of Kennametal Inc.
- Teflon is a registered a trademark of The Chemours Company FC, LLC